United Abrasives’ brushes consist of only the highest grade industrial tempered wire and state-of-the-art construction, designed for off-hand equipment. The various styles cover a multitude of applications.
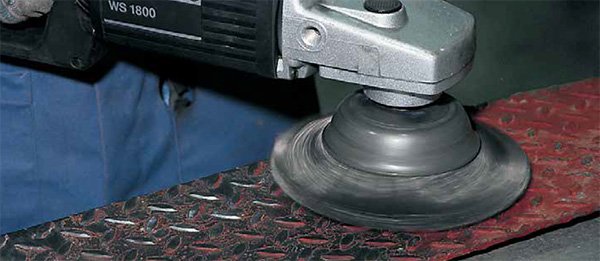
Features and Benefits
Brushes are available in a variety of wire types. The proper brush for the application should be selected based on the characteristics of the brush, including wire type. All BlueLine™ packaging is one piece per package.
Knot wire brushes provide high impact action and offer low to medium flexibility through the use of twisted wire tufts for heavy duty applications, such as weld cleaning. Knot wire brushes are available in 2 knot configurations.
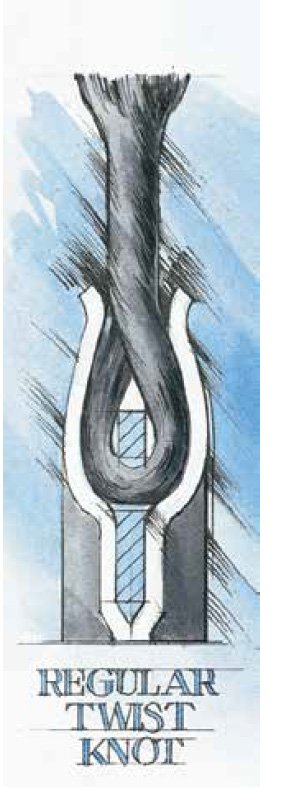
Flag at end of wire tuft provides additional brush flexibility for irregular surface preparation.
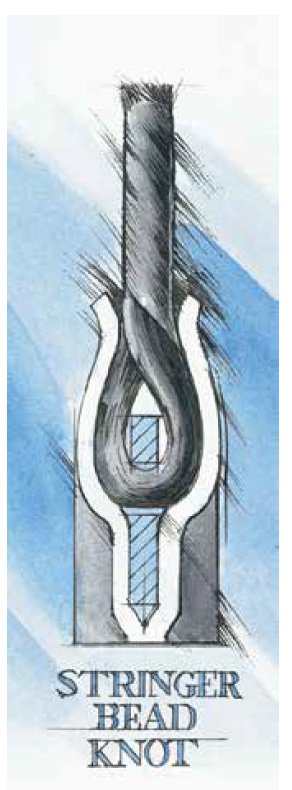
Extremely narrow tufted face is ideal for bead weld preparation.
Crimped wire brushes are general purpose brushes that provide higher flexibility and cleaning action through the use of flexible wire points. They offer a wider work face than knot style and are ideal for light applications such as rust or paint removal.
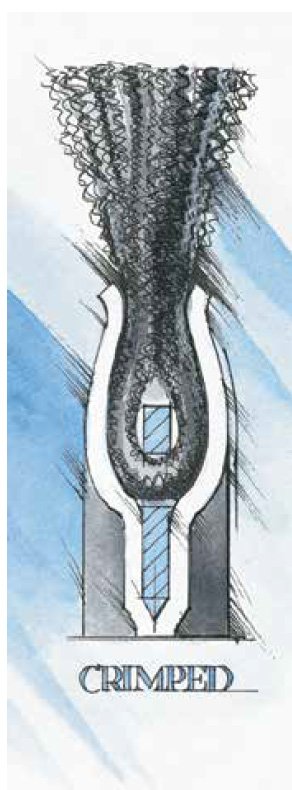
Flexible wire points provide cleaning action for light applications.
Wire Size Specifications
The thickness of brush wire will impact the end result of the workpiece. Fine wire such as .008 will produce a finer finish and will yield a longer brush life. Thicker wires, such as .014 and .020 or higher, will be more aggressive and will decrease production times.
Brush Fill Materials
Carbon steel, the most durable, high strength fill material available for general purpose cleaning applications, is suitable for light to heavy duty cleaning depending on the wire diameter.
Stainless Steel fill material is suitable on metals such as aluminum and stainless steel when corrosion resistance and
non-contaminant brushing actions are desired.
Application Information
- Always check warning labels for safety information
- Always follow safety guidelines included with each brush package
- Proper application of wire brushes is for the removal of various surface contaminants, not the removal of the base stock material
- The power tool determines the size and speed of the brush to be used
- Check the R.P.M. rating of the tool to verify that it does not exceed the Maximum Safe Free Speed (M.S.F.S.) of the brush
- The slowest speed that will do the job is the most efficient use of the brush. Running at the M.S.F.S. is not necessarily the most efficient speed
- The tool shaft must match the arbor hole of the brush
- The tips of wire at the end of the brush do the work. Excessive pressure will cause premature wire breakage, reduced brush life, increased heat build-up and rapid dulling.
Power Brush Safety Requirements
- Safety Goggles: Safety goggles, or full face shields worn over safety glasses with side shields, MUST BE WORN by all OPERATORS and OTHERS IN THE AREA OF POWER BRUSH OPERATIONS. Comply with the requirements of ANSI Z87.1 (“Occupational Eye and Face Protection”).
- Guards: Keep all machine guards in place.
- Speeds: Observe all speed restrictions indicated on the brushes, containers, labels, or printed in pertinent literature. “MSFS” or “MAX.SFS” means Maximum Safe Free Speed (R.P.M.) – spinning free with no work applied. For reasons of safety, the “MSFS/MAX.SFS” should not be exceeded under any circumstances.
- Safety Standard: Comply with the safety standards of the American National Standards Institute, ANSI B165.1 and ANSI B165.2 – “Safety Requirements – Power Brushes.”
- Protective Equipment: Appropriate protective clothing and equipment (such as full face shield, gloves, respirator, etc.) must be used where a possibility of injury exists that can be prevented by such equipment.
- Before starting brush: Use eye protection and safety equipment. Inspect brush for rust, damage, speed limit, etc. If no-load speed marked on the power tool is higher than the brush speed limit, do not mount brush. Inspect and jog machine to assure the brush is mounted properly and securely, machine guards are in place, no vibration, etc. Run machine at operating speed for at least one minute before applying work. DO NOT STAND IN FRONT OF OR IN LINE WITH BRUSH.
Common Brush Terminology
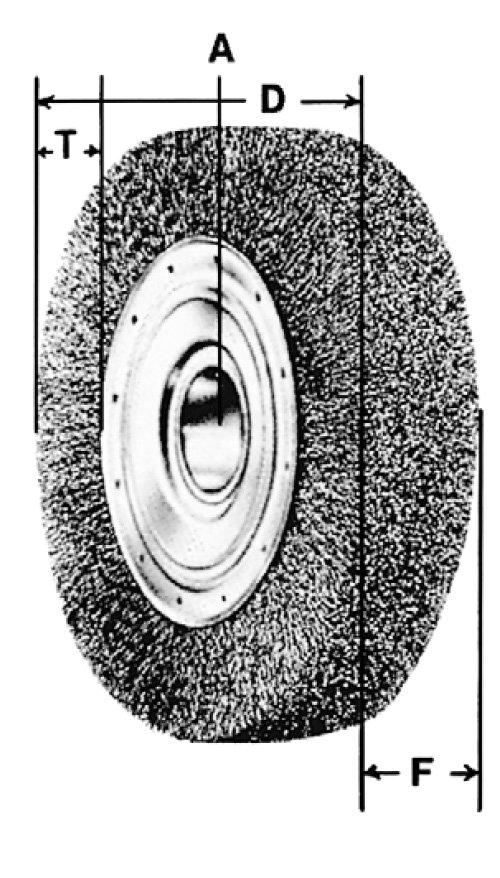
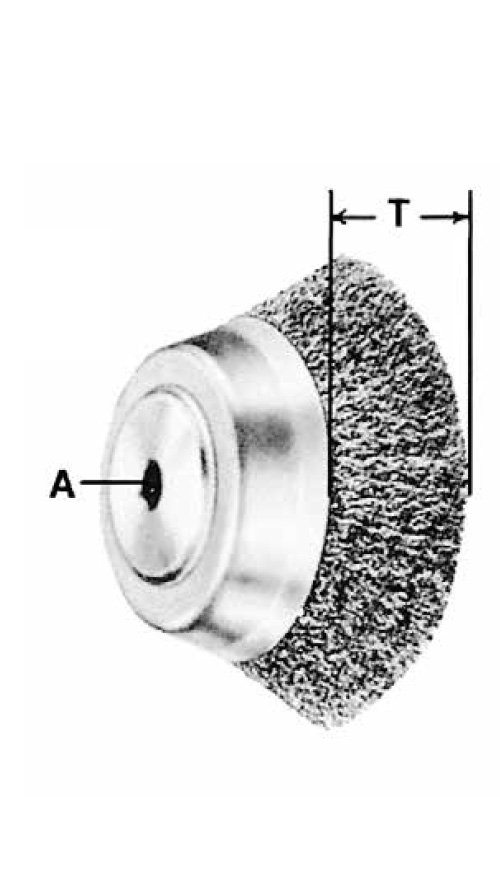